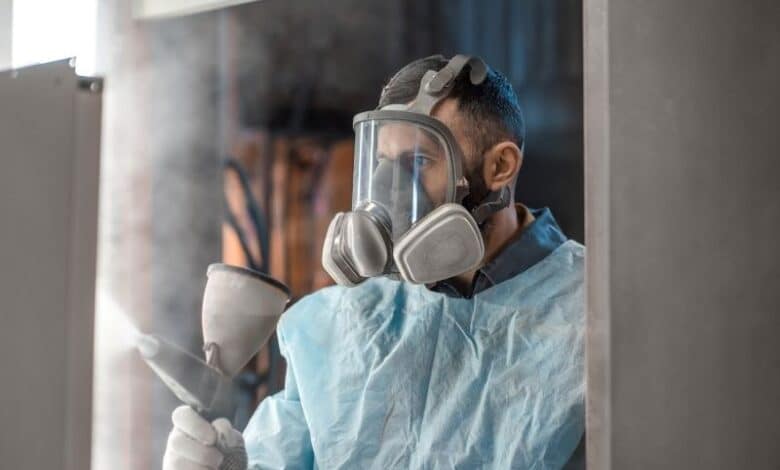
Powder coating is a widely used finishing process in the manufacturing industry, renowned for its durability, environmental benefits, and versatility. Unlike traditional liquid paint, which relies on solvents to keep the binder and filler parts in liquid suspension, powder coat involves the application of a dry powder onto a surface. This method has gained popularity due to its ability to produce a resilient and attractive finish on a variety of materials, including metal, plastic, and even wood.
One of the key advantages of powder coating is its sustainability. Unlike liquid paint, powder coatings emit virtually no volatile organic compounds (VOCs) into the atmosphere, making them an environmentally friendly choice. This not only reduces air pollution but also helps companies comply with strict environmental regulations. Additionally, powder coating materials are generally free from heavy metals, further enhancing their eco-friendliness.
Durability is another hallmark of powder coating. Once applied and cured, powder-coated surfaces are resistant to chipping, cracking, fading, and peeling, ensuring that the finish remains vibrant and intact for years to come. This durability makes powder coating an ideal choice for products exposed to harsh environmental conditions, such as outdoor furniture, automotive parts, and architectural elements.
The application process of powder coating is straightforward. First, the dry powder is electrostatically charged, causing it to adhere to the grounded object. This charged attraction ensures even coverage and minimizes waste. After coating, the item is heated in an oven, allowing the powder to melt and flow into a smooth, continuous film. This curing process results in a durable finish that is resistant to scratches and corrosion.
Moreover, powder coating offers a wide range of color options and finishes, from matte to glossy, textured to metallic, allowing manufacturers and designers to achieve their desired aesthetics. The versatility of this finishing method is further enhanced by its ability to create intricate patterns, logos, and designs on the coated surface.